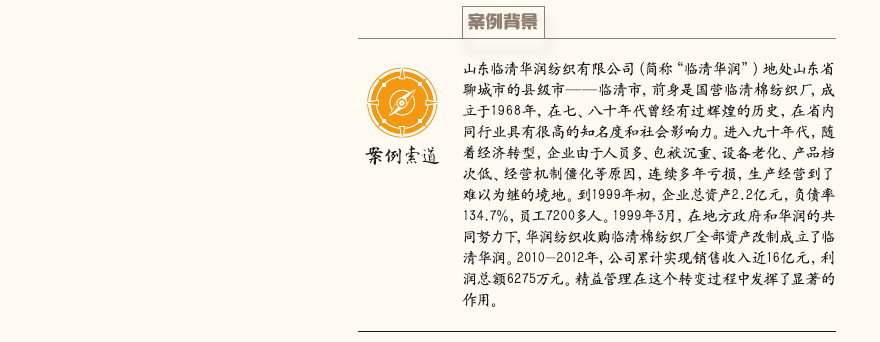
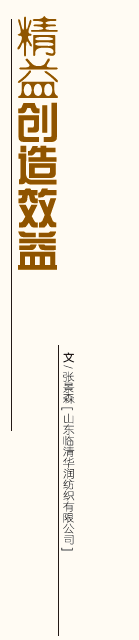
从外部看,行业市场形势处于近30年来的低谷,对行业复苏的预期不乐观。从内部看,公司多数设备陈旧老化,尤其是电气元件老化,正逐步进入故障频发期,制约生产效率;而管理人员仍沿袭传统管理手段,员工工作仍依靠经验传承,创新意识不足。要驱动棉纺企业调整转型、实现内涵增长,提升“精益运营能力”是在这种困境下我们必须要走的一条路。
然而,搞精益管理全员改善,和以前那些节约挖潜、金点子、小改小革、行动学习等等活动有什么区别?是不是也是个短期的阶段性任务?是不是都是管理人员和专业的设备、工艺人员的事,与普通员工有什么关系?对这类活动,员工心中普遍存有疑惑。
思想转变
在一次精益管理培训会召开的过程中,公司总经理袁总忽然向参训人员发问:“大家现在看看我们这间教室里面,有没有浪费和可以改善的地方?”
参会人员环顾四周,面面相觑,互相摇头。
袁总接着说:“公司规定办公场所、会议室室温在12℃以上禁开热风,30℃以下禁开冷风,室内都挂有温度计。”顺着袁总指的方向看过去,墙上的确挂着一支温度计。“这种温度计既能看温度,又能看湿度,价格大约160-170元,是车间必备的;而办公场所、会议室只看温度就可以了,完全可以用那种很简单的价格不到10元的温度计代替。这种温度计放在这个位置,大材小用,就是一种浪费,就需要改善,这就是精益思维、精益理念。”
听完这番话,大家恍然大悟,精益思维和理念并不复杂,精益管理就是要“消除一切形式的浪费”,并且亲自动手去改善。
现场实战
随后,公司开始举办“华润纺织精益六西格玛专家训练营”,并请学员学完回到公司后转训,让这批学员成为精益管理项目推进的催化剂。
培训中学员常常被问及的问题包括:“谁知道最新上调的电价是多少钱一度?电价的峰谷平的具体时段?”、“我们每台细纱机、织布机每月机物料消耗是多少?其中什么机配件消耗最多?”、“我们公司一个月消耗多少吨原棉、多少度电?”、“我们在机生产的品种,有多少是高利润的?”
带着这些问题,学员深入车间现场,打开思路、擦亮眼睛,寻找浪费点、标识不清、安全隐患、质量隐患等可以改进的事项。一次现场查找1小时后,各小组学员返回培训室汇总,删去重复项目后,找到的问题仍高达50多项,而且大部分都是大家此前习以为常的问题。
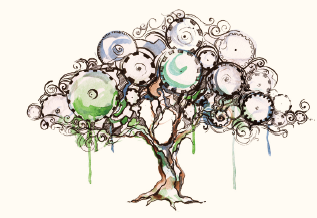
在实践中学习,在学习中实干,一段时间后,公司上下,包括一线员工都感受到这次与以前相比真的不一样了。领导们都很重视,从公司一把手到各分管高管,再到车间主管、班组长,层层培训、级级学习。车间还专门设置了“改善墙”,导入了许多新名词:Kaizen、SGA、SDA、KPI、“五现主义”、分层别、找偏差、由果寻因等等,大家对精益管理逐渐有了感觉。
体系保障
不把精益管理搞成一场运动式的突击,而是要让精益管理成为系统工程,实现良性发展,落地生根,成为了所有人的共识。为了这一目标,临清华润2012年建立了“组织保障、宣导培训、人才队伍和精益激励”四大工作体系,为全面推动精益管理提供组织保障。
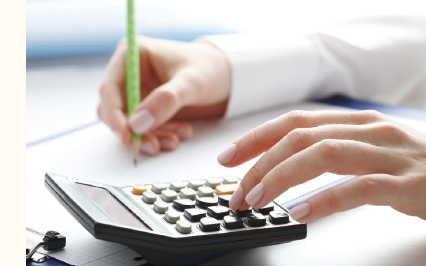
为调动不同层次人员的积极性,公司把精益改善成果作为评价员工绩效的一个重要因素。根据成果贡献大小,分别给予表扬、奖励和晋级,为员工展示才能提供平台,为员工成长进步创造平等机会。
遍地开花
根据改善涉及的人员和参与部门的范围不同,临清华润的精益管理改善分为Kaizen(全员改善活动)、SGA(小组改善活动)和SDA(技能开发活动)三个不同的维度。
全员参与,班组基层抓Kaizen。为使精益管理在基层班组落地生根,激发全员智慧和创造力,公司在基层班组原有的信息员、安全员的基础上,增设231名Kaizen改善引导员,形成班组日常管理工作的“三大员”,成为夯实班组建设的三支重要力量。2012年9-12月底,累计Kaizen提案达到5678项。2013年1-6月,公司Kaizen总件数完成7740件。
中层推进,技术人员做SGA。公司要求中层牵头,组织工段长、工程师以上人员抓SGA项目,重点围绕“提升质量、提速提效,降低系统成本、机物料消耗和解决生产中的疑难问题”展开,强调运用精益方法论和简单工具,做“短平快”项目,不教条,不刻意“秀工具”,注重实际效果和价值创造。这一推动策略,为公司稳定质量、提升效率、降低系统成本等工作发挥了重要作用。 2013年1-6月,SGA项目注册153个,结案129个,结案率达到84.3%,创造直接经济效益74万元。
高管牵头,配置资源和力量攻SDA。公司要求,SDA项目必须规范运行,运用八步法及较为复杂的统计分析工具,不贪多、不求快,先易后难,循序渐进,重点是理解并熟练掌握方法和工具,培养逻辑思考、分析问题的能力,以及根据分析结论制定对策的行为习惯,逐步摆脱传统经验决策的思维定势。在每年进行业绩指标分解时,梳理聚焦影响业绩达成的关键KPI指标,通过对标确定改善目标,生成SDA项目。2012年至今年6月,公司共在集团注册了“降低千锭时断头、提高下机一等品率、降低机物料消耗”3个SDA项目。
收获体会
公司通过导入精益理念,提升改善技能,消除浪费点、改进流程作业及层别推进Kaizen、SGA、SDA,使总体运营质量和水平有了明显提升,也让所有人对精益管理运营有了更切身的体会。
精益管理要结合企业面临的实际情况,层别展开精益改善。精益管理是一个循序渐进、持续提升的过程,绝非朝夕之功。Kaizen启动展开阶段,我们注重Kaizen数量多少,不在乎质量高低和项目的大小,强调“改善不怕小,重在参与”,营造全员参与的氛围;SGA、SDA项目展开不求快,而是追求方法和工具的理解运用,循序渐进,侧重培养员工的逻辑思考、分析问题的能力,以及根据分析结论制定对策的行为习惯,逐步摆脱传统经验决策的思维定势。
回顾项目过程,设立班组“三大员”是Kaizen在基层班组落地的有效手段,一把手是否重视是推进项目落地的重要条件。在此基础上,借助科学系统的方法论作为指导、精益专业的人才队伍作为支撑,“强化宣导培训,营造精益氛围”,最终培育了整个公司的精益文化,让精益思维成为了员工自动自发的日常行为习惯。
三年来,临清华润通过深化两个机制建设、推行精益管理,管理团队管理行为和工作作风有了转变,团队战斗力、执行力增强,促进了淘汰落后产能、优化用工和业务调整转型,多年来困扰企业发展的历史遗留问题逐步得到解决,企业组织能力有了明显提升。但与集团要求相比,目前仍有较大差距。集团棉纺企业仍处在调整转型期,特别是行业形势仍没有向好迹象,严酷的生存现实,逼迫我们必须深刻反思,必须进一步提升企业的组织能力。下一步我们将按照纺织集团的工作要求,不断细化落实各项举措,在深化团队建设、塑造组织能力方面继续不懈努力,而精益管理工作将依照《临清华润精益管理三年规划(2012-2014)》继续扎实稳步推进,力争取得更大的成绩。
